12V DC motor speed controller. Powerful PWM regulator. The principle of operation of a transistor regulator
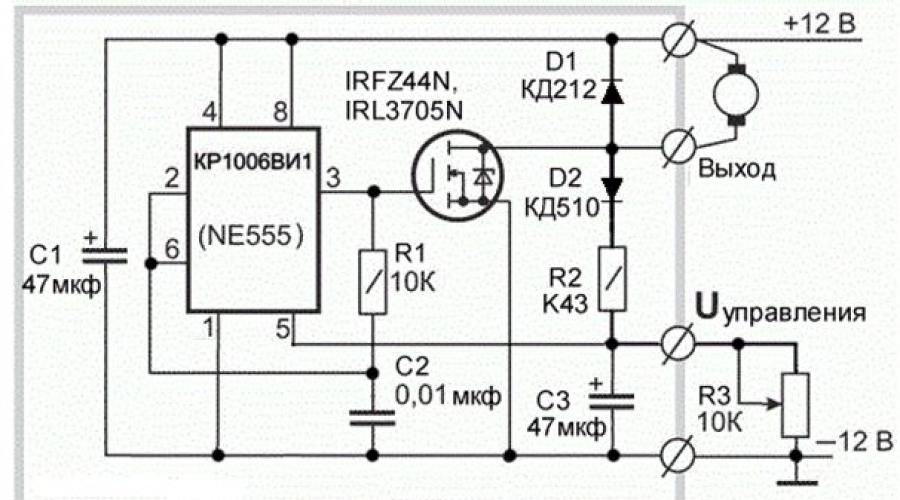
To smoothly increase and decrease the shaft rotation speed, there is a special device - a 220V electric motor speed controller. Stable operation, no voltage interruptions, long service life - the advantages of using an engine speed controller for 220, 12 and 24 volts.
- Application area
- Selecting a device
- IF device
- Types of devices
- Triac device
Why do you need a frequency converter?
The function of the regulator is to invert the voltage of 12, 24 volts, ensuring smooth start and stop using pulse width modulation.
Speed controllers are included in the structure of many devices, as they ensure the accuracy of electrical control. This allows you to adjust the speed to the desired amount.
Application area
DC motor speed controller is used in many industrial and domestic applications. For example:
- heating complex;
- equipment drives;
- welding machine;
- electric ovens;
- vacuum cleaners;
- Sewing machines;
- washing machines.
Selecting a device
In order to select an effective regulator, it is necessary to take into account the characteristics of the device and its intended purpose.
- Vector controllers are common for commutator motors, but scalar controllers are more reliable.
- An important selection criterion is power. It must correspond to that permitted on the unit used. It is better to exceed for safe operation of the system.
- The voltage must be within acceptable wide ranges.
- The main purpose of the regulator is to convert frequency, so this aspect must be selected according to the technical requirements.
- You also need to pay attention to the service life, dimensions, number of inputs.
IF device
- AC motor natural controller;
- drive unit;
- additional elements.
The circuit diagram of the 12 V engine speed controller is shown in the figure. The speed is adjusted using a potentiometer. If pulses with a frequency of 8 kHz are received at the input, then the supply voltage will be 12 volts.
The device can be purchased at specialized sales points, or you can make it yourself.
When starting a three-phase motor at full power, current is transmitted, the action is repeated about 7 times. The current bends the motor windings, generating heat over a long period of time. A converter is an inverter that provides energy conversion. The voltage enters the regulator, where 220 volts are rectified using a diode located at the input. Then the current is filtered through 2 capacitors. PWM is generated. Next, the pulse signal is transmitted from the motor windings to a specific sinusoid.
There is a universal 12V device for brushless motors.
To save on electricity bills, our readers recommend the Electricity Saving Box. Monthly payments will be 30-50% less than they were before using the saver. It removes the reactive component from the network, resulting in a reduction in load and, as a consequence, current consumption. Electrical appliances consume less electricity and costs are reduced.
The circuit consists of two parts - logical and power. The microcontroller is located on a chip. This scheme is typical for a powerful engine. The uniqueness of the regulator lies in its use with various types of engines. The circuits are powered separately; the key drivers require 12V power.
Types of devices
Triac device
The triac device is used to control lighting, power of heating elements, and rotation speed.
The controller circuit based on a triac contains a minimum of parts shown in the figure, where C1 is a capacitor, R1 is the first resistor, R2 is the second resistor.
Using a converter, power is regulated by changing the time of an open triac. If it is closed, the capacitor is charged by the load and resistors. One resistor controls the amount of current, and the second regulates the charging rate.
When the capacitor reaches the maximum voltage threshold of 12V or 24V, the switch is activated. The triac goes into the open state. When the mains voltage passes through zero, the triac is locked, and then the capacitor gives a negative charge.
Converters on electronic keys
Common thyristor regulators with a simple operating circuit.
Thyristor, works in alternating current network.
A separate type is the AC voltage stabilizer. The stabilizer contains a transformer with numerous windings.
To a 24 volt voltage source. The principle of operation is to charge a capacitor and a locked thyristor, and when the capacitor reaches voltage, the thyristor sends current to the load.
Proportional Signal Process
Signals arriving at the system input form feedback. Let's take a closer look using a microcircuit.
The TDA 1085 chip pictured above provides feedback control of a 12V, 24V motor without loss of power. It is mandatory to contain a tachometer, which provides feedback from the engine to the control board. The stabilization sensor signal goes to a microcircuit, which transmits the task to the power elements - to add voltage to the motor. When the shaft is loaded, the board increases the voltage and the power increases. By releasing the shaft, the tension decreases. The revolutions will be constant, but the power torque will not change. The frequency is controlled over a wide range. Such a 12, 24 volt motor is installed in washing machines.
With your own hands you can make a device for a grinder, wood lathe, sharpener, concrete mixer, straw cutter, lawn mower, wood splitter and much more.
Industrial regulators, consisting of 12, 24 volt controllers, are filled with resin and therefore cannot be repaired. Therefore, a 12V device is often made independently. A simple option using the U2008B chip. The controller uses current feedback or soft start. If the latter is used, elements C1, R4 are required, jumper X1 is not needed, but with feedback, vice versa.
When assembling the regulator, choose the right resistor. Since with a large resistor there may be jerks at the start, and with a small resistor the compensation will be insufficient.
Important! When adjusting the power controller, you need to remember that all parts of the device are connected to the AC network, so safety precautions must be observed!
Speed controllers for single-phase and three-phase 24, 12 volt motors are a functional and valuable device, both in everyday life and in industry.
On simple mechanisms it is convenient to install analog current regulators. For example, they can change the speed of rotation of the motor shaft. From the technical side, implementing such a regulator is simple (you will need to install one transistor). Suitable for adjusting independent speed of motors in robotics and power supplies. The most common types of regulators are single-channel and two-channel.
Video No. 1. Single-channel regulator in operation. Changes the rotation speed of the motor shaft by rotating the variable resistor knob.
Video No. 2. Increasing the rotation speed of the motor shaft when operating a single-channel regulator. An increase in the number of revolutions from the minimum to the maximum value when rotating the variable resistor knob.
Video No. 3. Two-channel regulator in operation. Independent setting of the torsion speed of motor shafts based on trimming resistors.
Video No. 4. The voltage at the output of the regulator was measured with a digital multimeter. The resulting value is equal to the battery voltage, from which 0.6 volts have been subtracted (the difference arises due to the voltage drop across the transistor junction). When using a 9.55 volt battery, a change from 0 to 8.9 volts is recorded.
Functions and main characteristics
The load current of single-channel (photo 1) and two-channel (photo 2) regulators does not exceed 1.5 A. Therefore, to increase the load capacity, the KT815A transistor is replaced with KT972A. The numbering of the pins for these transistors is the same (e-k-b). But the KT972A model is operational with currents up to 4A.
Single channel motor controller
The device controls one motor, powered by voltage in the range from 2 to 12 volts.
Device design
The main design elements of the regulator are shown in the photo. 3. The device consists of five components: two variable resistance resistors with a resistance of 10 kOhm (No. 1) and 1 kOhm (No. 2), a transistor model KT815A (No. 3), a pair of two-section screw terminal blocks for the output for connecting a motor (No. 4) and input for connecting a battery (No. 5).
Note 1. Installation of screw terminal blocks is not necessary. Using a thin stranded mounting wire, you can connect the motor and power source directly.
Principle of operation
The operating procedure of the motor controller is described in the electrical diagram (Fig. 1). Taking into account the polarity, a constant voltage is supplied to the XT1 connector. The light bulb or motor is connected to the XT2 connector. A variable resistor R1 is turned on at the input; rotating its knob changes the potential at the middle output as opposed to the minus of the battery. Through current limiter R2, the middle output is connected to the base terminal of transistor VT1. In this case, the transistor is switched on according to a regular current circuit. The positive potential at the base output increases as the middle output moves upward from the smooth rotation of the variable resistor knob. There is an increase in current, which is due to a decrease in the resistance of the collector-emitter junction in transistor VT1. The potential will decrease if the situation is reversed.

Materials and details
A printed circuit board measuring 20x30 mm is required, made of a fiberglass sheet foiled on one side (permissible thickness 1-1.5 mm). Table 1 provides a list of radio components.
Note 2. The variable resistor required for the device can be of any manufacture; it is important to observe the current resistance values for it indicated in Table 1.
Note 3. To regulate currents above 1.5A, the KT815G transistor is replaced with a more powerful KT972A (with a maximum current of 4A). In this case, the printed circuit board design does not need to be changed, since the distribution of pins for both transistors is identical.
Build process
For further work, you need to download the archive file located at the end of the article, unzip it and print it. The regulator drawing (file) is printed on glossy paper, and the installation drawing (file) is printed on a white office sheet (A4 format).
Next, the drawing of the circuit board (No. 1 in photo. 4) is glued to the current-carrying tracks on the opposite side of the printed circuit board (No. 2 in photo. 4). It is necessary to make holes (No. 3 in photo. 14) on the installation drawing in the mounting locations. The installation drawing is attached to the printed circuit board with dry glue, and the holes must match. Photo 5 shows the pinout of the KT815 transistor.
The input and output of terminal blocks-connectors are marked in white. A voltage source is connected to the terminal block via a clip. A fully assembled single-channel regulator is shown in the photo. The power source (9 volt battery) is connected at the final stage of assembly. Now you can adjust the shaft rotation speed using the motor; to do this, you need to smoothly rotate the variable resistor adjustment knob.
To test the device, you need to print a disk drawing from the archive. Next, you need to paste this drawing (No. 1) onto thick and thin cardboard paper (No. 2). Then, using scissors, a disc is cut out (No. 3).
The resulting workpiece is turned over (No. 1) and a square of black electrical tape (No. 2) is attached to the center for better adhesion of the surface of the motor shaft to the disk. You need to make a hole (No. 3) as shown in the image. Then the disk is installed on the motor shaft and testing can begin. The single-channel motor controller is ready!
Two-channel motor controller
Used to independently control a pair of motors simultaneously. Power is supplied from a voltage ranging from 2 to 12 volts. The load current is rated up to 1.5A per channel.
Device design
The main components of the design are shown in photo.10 and include: two trimming resistors for adjusting the 2nd channel (No. 1) and the 1st channel (No. 2), three two-section screw terminal blocks for output to the 2nd motor (No. 3), for output to the 1st motor (No. 4) and for input (No. 5).
Note:1 Installation of screw terminal blocks is optional. Using a thin stranded mounting wire, you can connect the motor and power source directly.
Principle of operation
The circuit of a two-channel regulator is identical to the electrical circuit of a single-channel regulator. Consists of two parts (Fig. 2). The main difference: the variable resistance resistor is replaced with a trimming resistor. The rotation speed of the shafts is set in advance.
Note.2. To quickly adjust the rotation speed of the motors, the trimming resistors are replaced using a mounting wire with variable resistance resistors with the resistance values indicated in the diagram.
Materials and details
You will need a printed circuit board measuring 30x30 mm, made of a fiberglass sheet foiled on one side with a thickness of 1-1.5 mm. Table 2 provides a list of radio components.
Build process
After downloading the archive file located at the end of the article, you need to unzip it and print it. The regulator drawing for thermal transfer (termo2 file) is printed on glossy paper, and the installation drawing (montag2 file) is printed on a white office sheet (A4 format).
The circuit board drawing is glued to the current-carrying tracks on the opposite side of the printed circuit board. Form holes on the installation drawing in the mounting locations. The installation drawing is attached to the printed circuit board with dry glue, and the holes must match. The KT815 transistor is being pinned. To check, you need to temporarily connect inputs 1 and 2 with a mounting wire.
Any of the inputs is connected to the pole of the power source (a 9-volt battery is shown in the example). The negative of the power supply is attached to the center of the terminal block. It is important to remember: the black wire is “-” and the red wire is “+”.
The motors must be connected to two terminal blocks, and the desired speed must also be set. After successful testing, you need to remove the temporary connection of the inputs and install the device on the robot model. The two-channel motor controller is ready!
The necessary diagrams and drawings for the work are presented. The emitters of the transistors are marked with red arrows.
This DIY circuit can be used as a speed controller for a 12V DC motor with a current rating of up to 5A, or as a dimmer for 12V halogen and LED lamps up to 50W. Control is carried out using pulse width modulation (PWM) at a pulse repetition rate of about 200 Hz. Naturally, the frequency can be changed if necessary, selecting for maximum stability and efficiency.
Most of these structures are assembled according to a much simpler scheme. Here we present a more advanced version that uses a 7555 timer, a bipolar transistor driver and a powerful MOSFET. This design provides improved speed control and operates over a wide load range. This is indeed a very effective scheme and the cost of its parts when purchased for self-assembly is quite low.
PWM controller circuit for 12 V motor
The circuit uses a 7555 Timer to create a variable pulse width of about 200 Hz. It controls transistor Q3 (via transistors Q1 - Q2), which controls the speed of the electric motor or light bulbs.
There are many applications for this circuit that will be powered by 12V: electric motors, fans or lamps. It can be used in cars, boats and electric vehicles, in model railways and so on.
12 V LED lamps, for example LED strips, can also be safely connected here. Everyone knows that LED bulbs are much more efficient than halogen or incandescent bulbs and will last much longer. And if necessary, power the PWM controller from 24 volts or more, since the microcircuit itself with a buffer stage has a power stabilizer.
AC Motor Speed Controller
PWM controller 12 volt
Half Bridge DC Regulator Driver
Mini drill speed controller circuit
ENGINE SPEED CONTROL WITH REVERSE
Hello everyone, probably many radio amateurs, like me, have more than one hobby, but several. In addition to designing electronic devices, I do photography, video shooting with a DSLR camera, and video editing. As a videographer, I needed a slider for video shooting, and first I’ll briefly explain what it is. The photo below shows the factory slider.
The slider is designed for video shooting on cameras and video cameras. It is analogous to the rail system used in wide-format cinema. With its help, a smooth movement of the camera around the object being photographed is created. Another very powerful effect that can be used when working with a slider is the ability to move closer or further from the subject. The next photo shows the engine that was chosen to make the slider.
The slider is driven by a 12-volt DC motor. A diagram of a regulator for the motor that moves the slider carriage was found on the Internet. The next photo shows the power indicator on the LED, the toggle switch that controls the reverse and the power switch.
When operating such a device, it is important that there is smooth speed control, plus easy inclusion of engine reverse. The speed of rotation of the motor shaft, in the case of using our regulator, is smoothly adjusted by rotating the knob of a 5 kOhm variable resistor. Perhaps I am not the only one of the users of this site who is interested in photography, and someone else will want to replicate this device; those who wish can download an archive with a circuit diagram and printed circuit board of the regulator at the end of the article. The following figure shows a schematic diagram of a regulator for an engine:
Regulator circuit
The circuit is very simple and can be easily assembled even by novice radio amateurs. Among the advantages of assembling this device, I can name its low cost and the ability to customize it to meet your needs. The figure shows the controller's printed circuit board:
But the scope of application of this regulator is not limited to sliders alone; it can easily be used as a speed regulator, for example, a machine drill, a homemade Dremel powered by 12 volts, or a computer cooler, for example, with dimensions of 80 x 80 or 120 x 120 mm. I also developed a scheme for reversing the engine, or in other words, quickly changing the rotation of the shaft in the other direction. To do this, I used a six-pin toggle switch with 2 positions. The following figure shows its connection diagram:
The middle contacts of the toggle switch, marked (+) and (-), are connected to the contacts on the board marked M1.1 and M1.2, the polarity does not matter. Everyone knows that computer coolers, when the supply voltage and, accordingly, the speed are reduced, make much less noise during operation. In the next photo, the KT805AM transistor is on the radiator:
Almost any medium and high power n-p-n structure transistor can be used in the circuit. The diode can also be replaced with analogues suitable for the current, for example 1N4001, 1N4007 and others. The motor terminals are shunted by a diode in reverse connection; this was done to protect the transistor during switch-on and switch-off moments of the circuit, since our motor has an inductive load. Also, the circuit provides an indication that the slider is turned on on an LED connected in series with a resistor.
When using an engine of greater power than shown in the photo, the transistor must be attached to the radiator to improve cooling. A photo of the resulting board is shown below:
The regulator board was manufactured using the LUT method. You can see what happened in the end in the video.
Video of work
Soon, as soon as the missing parts, mainly mechanics, are acquired, I will begin assembling the device in the case. Sent the article Alexey Sitkov .
Diagrams and overview of 220V electric motor speed controllers
To smoothly increase and decrease the shaft rotation speed, there is a special device - a 220V electric motor speed controller. Stable operation, no voltage interruptions, long service life - the advantages of using an engine speed controller for 220, 12 and 24 volts.
- Why do you need a frequency converter?
- Application area
- Selecting a device
- IF device
- Types of devices
- Triac device
- Proportional Signal Process
Why do you need a frequency converter?
The function of the regulator is to invert the voltage of 12, 24 volts, ensuring smooth start and stop using pulse width modulation.
Speed controllers are included in the structure of many devices, as they ensure the accuracy of electrical control. This allows you to adjust the speed to the desired amount.
Application area
DC motor speed controller is used in many industrial and domestic applications. For example:
- heating complex;
- equipment drives;
- welding machine;
- electric ovens;
- vacuum cleaners;
- Sewing machines;
- washing machines.
Selecting a device
In order to select an effective regulator, it is necessary to take into account the characteristics of the device and its intended purpose.
- Vector controllers are common for commutator motors, but scalar controllers are more reliable.
- An important selection criterion is power. It must correspond to that permitted on the unit used. It is better to exceed for safe operation of the system.
- The voltage must be within acceptable wide ranges.
- The main purpose of the regulator is to convert frequency, so this aspect must be selected according to the technical requirements.
- You also need to pay attention to the service life, dimensions, number of inputs.
IF device
- AC motor natural controller;
- drive unit;
- additional elements.
The circuit diagram of the 12 V engine speed controller is shown in the figure. The speed is adjusted using a potentiometer. If pulses with a frequency of 8 kHz are received at the input, then the supply voltage will be 12 volts.
The device can be purchased at specialized sales points, or you can make it yourself.
AC speed controller circuit
When starting a three-phase motor at full power, current is transmitted, the action is repeated about 7 times. The current bends the motor windings, generating heat over a long period of time. A converter is an inverter that provides energy conversion. The voltage enters the regulator, where 220 volts are rectified using a diode located at the input. Then the current is filtered through 2 capacitors. PWM is generated. Next, the pulse signal is transmitted from the motor windings to a specific sinusoid.
There is a universal 12V device for brushless motors.
To save on electricity bills, our readers recommend the Electricity Saving Box. Monthly payments will be 30-50% less than they were before using the saver. It removes the reactive component from the network, resulting in a reduction in load and, as a consequence, current consumption. Electrical appliances consume less electricity and costs are reduced.
The circuit consists of two parts - logical and power. The microcontroller is located on a chip. This scheme is typical for a powerful engine. The uniqueness of the regulator lies in its use with various types of engines. The circuits are powered separately; the key drivers require 12V power.
Types of devices
Triac device
The triac device is used to control lighting, power of heating elements, and rotation speed.
The controller circuit based on a triac contains a minimum of parts shown in the figure, where C1 is a capacitor, R1 is the first resistor, R2 is the second resistor.
Using a converter, power is regulated by changing the time of an open triac. If it is closed, the capacitor is charged by the load and resistors. One resistor controls the amount of current, and the second regulates the charging rate.
When the capacitor reaches the maximum voltage threshold of 12V or 24V, the switch is activated. The triac goes into the open state. When the mains voltage passes through zero, the triac is locked, and then the capacitor gives a negative charge.
Converters on electronic keys
Common thyristor regulators with a simple operating circuit.
Thyristor, works in alternating current network.
A separate type is the AC voltage stabilizer. The stabilizer contains a transformer with numerous windings.
DC stabilizer circuit
24 volt thyristor charger
To a 24 volt voltage source. The principle of operation is to charge a capacitor and a locked thyristor, and when the capacitor reaches voltage, the thyristor sends current to the load.
Proportional Signal Process
Signals arriving at the system input form feedback. Let's take a closer look using a microcircuit.
Chip TDA 1085
The TDA 1085 chip pictured above provides feedback control of a 12V, 24V motor without loss of power. It is mandatory to contain a tachometer, which provides feedback from the engine to the control board. The stabilization sensor signal goes to a microcircuit, which transmits the task to the power elements - to add voltage to the motor. When the shaft is loaded, the board increases the voltage and the power increases. By releasing the shaft, the tension decreases. The revolutions will be constant, but the power torque will not change. The frequency is controlled over a wide range. Such a 12, 24 volt motor is installed in washing machines.
With your own hands you can make a device for a grinder, wood lathe, sharpener, concrete mixer, straw cutter, lawn mower, wood splitter and much more.
Industrial regulators, consisting of 12, 24 volt controllers, are filled with resin and therefore cannot be repaired. Therefore, a 12V device is often made independently. A simple option using the U2008B chip. The controller uses current feedback or soft start. If the latter is used, elements C1, R4 are required, jumper X1 is not needed, but with feedback, vice versa.
When assembling the regulator, choose the right resistor. Since with a large resistor there may be jerks at the start, and with a small resistor the compensation will be insufficient.
Important! When adjusting the power controller, you need to remember that all parts of the device are connected to the AC network, so safety precautions must be observed!
Speed controllers for single-phase and three-phase 24, 12 volt motors are a functional and valuable device, both in everyday life and in industry.
Rotation controller for motor
On simple mechanisms it is convenient to install analog current regulators. For example, they can change the speed of rotation of the motor shaft. From the technical side, implementing such a regulator is simple (you will need to install one transistor). Suitable for adjusting independent speed of motors in robotics and power supplies. The most common types of regulators are single-channel and two-channel.
Video No. 1. Single-channel regulator in operation. Changes the rotation speed of the motor shaft by rotating the variable resistor knob.
Video No. 2. Increasing the rotation speed of the motor shaft when operating a single-channel regulator. An increase in the number of revolutions from the minimum to the maximum value when rotating the variable resistor knob.
Video No. 3. Two-channel regulator in operation. Independent setting of the torsion speed of motor shafts based on trimming resistors.
Video No. 4. The voltage at the output of the regulator was measured with a digital multimeter. The resulting value is equal to the battery voltage, from which 0.6 volts have been subtracted (the difference arises due to the voltage drop across the transistor junction). When using a 9.55 volt battery, a change from 0 to 8.9 volts is recorded.
Functions and main characteristics
The load current of single-channel (photo 1) and two-channel (photo 2) regulators does not exceed 1.5 A. Therefore, to increase the load capacity, the KT815A transistor is replaced with KT972A. The numbering of the pins for these transistors is the same (e-k-b). But the KT972A model is operational with currents up to 4A.
Single channel motor controller
The device controls one motor, powered by voltage in the range from 2 to 12 volts.
Device design
The main design elements of the regulator are shown in the photo. 3. The device consists of five components: two variable resistance resistors with a resistance of 10 kOhm (No. 1) and 1 kOhm (No. 2), a transistor model KT815A (No. 3), a pair of two-section screw terminal blocks for the output for connecting a motor (No. 4) and input for connecting a battery (No. 5).
Note 1. Installation of screw terminal blocks is not necessary. Using a thin stranded mounting wire, you can connect the motor and power source directly.
Principle of operation
The operating procedure of the motor controller is described in the electrical diagram (Fig. 1). Taking into account the polarity, a constant voltage is supplied to the XT1 connector. The light bulb or motor is connected to the XT2 connector. A variable resistor R1 is turned on at the input; rotating its knob changes the potential at the middle output as opposed to the minus of the battery. Through current limiter R2, the middle output is connected to the base terminal of transistor VT1. In this case, the transistor is switched on according to a regular current circuit. The positive potential at the base output increases as the middle output moves upward from the smooth rotation of the variable resistor knob. There is an increase in current, which is due to a decrease in the resistance of the collector-emitter junction in transistor VT1. The potential will decrease if the situation is reversed.
Electrical circuit diagram
Materials and details
A printed circuit board measuring 20x30 mm is required, made of a fiberglass sheet foiled on one side (permissible thickness 1-1.5 mm). Table 1 provides a list of radio components.
Note 2. The variable resistor required for the device can be of any manufacture; it is important to observe the current resistance values for it indicated in Table 1.
Note 3. To regulate currents above 1.5A, the KT815G transistor is replaced with a more powerful KT972A (with a maximum current of 4A). In this case, the printed circuit board design does not need to be changed, since the distribution of pins for both transistors is identical.
Build process
For further work, you need to download the archive file located at the end of the article, unzip it and print it. The regulator drawing (termo1 file) is printed on glossy paper, and the installation drawing (montag1 file) is printed on a white office sheet (A4 format).
Next, the drawing of the circuit board (No. 1 in photo. 4) is glued to the current-carrying tracks on the opposite side of the printed circuit board (No. 2 in photo. 4). It is necessary to make holes (No. 3 in photo. 14) on the installation drawing in the mounting locations. The installation drawing is attached to the printed circuit board with dry glue, and the holes must match. Photo 5 shows the pinout of the KT815 transistor.
The input and output of terminal blocks-connectors are marked in white. A voltage source is connected to the terminal block via a clip. A fully assembled single-channel regulator is shown in the photo. The power source (9 volt battery) is connected at the final stage of assembly. Now you can adjust the shaft rotation speed using the motor; to do this, you need to smoothly rotate the variable resistor adjustment knob.
To test the device, you need to print a disk drawing from the archive. Next, you need to paste this drawing (No. 1) onto thick and thin cardboard paper (No. 2). Then, using scissors, a disc is cut out (No. 3).
The resulting workpiece is turned over (No. 1) and a square of black electrical tape (No. 2) is attached to the center for better adhesion of the surface of the motor shaft to the disk. You need to make a hole (No. 3) as shown in the image. Then the disk is installed on the motor shaft and testing can begin. The single-channel motor controller is ready!
Two-channel motor controller
Used to independently control a pair of motors simultaneously. Power is supplied from a voltage ranging from 2 to 12 volts. The load current is rated up to 1.5A per channel.
The main components of the design are shown in photo.10 and include: two trimming resistors for adjusting the 2nd channel (No. 1) and the 1st channel (No. 2), three two-section screw terminal blocks for output to the 2nd motor (No. 3), for output to the 1st motor (No. 4) and for input (No. 5).
Note:1 Installation of screw terminal blocks is optional. Using a thin stranded mounting wire, you can connect the motor and power source directly.
Principle of operation
The circuit of a two-channel regulator is identical to the electrical circuit of a single-channel regulator. Consists of two parts (Fig. 2). The main difference: the variable resistance resistor is replaced with a trimming resistor. The rotation speed of the shafts is set in advance.
Note.2. To quickly adjust the rotation speed of the motors, the trimming resistors are replaced using a mounting wire with variable resistance resistors with the resistance values indicated in the diagram.
Materials and details
You will need a printed circuit board measuring 30x30 mm, made of a fiberglass sheet foiled on one side with a thickness of 1-1.5 mm. Table 2 provides a list of radio components.
Build process
After downloading the archive file located at the end of the article, you need to unzip it and print it. The regulator drawing for thermal transfer (termo2 file) is printed on glossy paper, and the installation drawing (montag2 file) is printed on a white office sheet (A4 format).
The circuit board drawing is glued to the current-carrying tracks on the opposite side of the printed circuit board. Form holes on the installation drawing in the mounting locations. The installation drawing is attached to the printed circuit board with dry glue, and the holes must match. The KT815 transistor is being pinned. To check, you need to temporarily connect inputs 1 and 2 with a mounting wire.
Any of the inputs is connected to the pole of the power source (a 9-volt battery is shown in the example). The negative of the power supply is attached to the center of the terminal block. It is important to remember: the black wire is “-” and the red wire is “+”.
The motors must be connected to two terminal blocks, and the desired speed must also be set. After successful testing, you need to remove the temporary connection of the inputs and install the device on the robot model. The two-channel motor controller is ready!
THE ARCHIVE contains the necessary diagrams and drawings for the work. The emitters of the transistors are marked with red arrows.
DC motor speed controller diagram
The DC motor speed controller circuit operates on the principles of pulse width modulation and is used to change the speed of a 12 volt DC motor. Regulating the engine shaft speed using pulse-width modulation gives greater efficiency than simply changing the DC voltage supplied to the engine, although we will also consider these schemes
DC motor speed controller circuit for 12 volts
The motor is connected in a circuit to a field-effect transistor which is controlled by pulse-width modulation carried out on the NE555 timer chip, which is why the circuit turned out to be so simple.
The PWM controller is implemented using a conventional pulse generator on an astable multivibrator, generating pulses with a repetition rate of 50 Hz and built on the popular NE555 timer. The signals coming from the multivibrator create a bias field at the gate of the field-effect transistor. The duration of the positive pulse is adjusted using variable resistance R2. The longer the duration of the positive pulse arriving at the gate of the field-effect transistor, the greater the power supplied to the DC motor. And vice versa, the shorter the pulse duration, the weaker the electric motor rotates. This circuit works great on a 12 volt battery.
DC motor speed control circuit for 6 volts
The speed of the 6 volt motor can be adjusted within 5-95%
Engine speed controller on PIC controller
Speed control in this circuit is achieved by applying voltage pulses of varying duration to the electric motor. For these purposes, PWM (pulse width modulators) are used. In this case, pulse width control is provided by a PIC microcontroller. To control the engine rotation speed, two buttons SB1 and SB2, “More” and “Less,” are used. You can change the rotation speed only when the “Start” toggle switch is pressed. The pulse duration varies, as a percentage of the period, from 30 to 100%.
As a voltage stabilizer for the PIC16F628A microcontroller, a three-pin KR1158EN5V stabilizer is used, which has a low input-output voltage drop, only about 0.6V. The maximum input voltage is 30V. All this allows the use of motors with voltages from 6V to 27V. The KT829A composite transistor is used as a power switch, which is preferably installed on a radiator.
The device is assembled on a printed circuit board measuring 61 x 52 mm. You can download the PCB drawing and firmware file from the link above. (See folder in the archive 027-el)
The simplest method of controlling the rotation speed of a DC motor is based on the use of pulse width modulation (PWM or PWM). The essence of this method is that the supply voltage is supplied to the motor in the form of pulses. In this case, the pulse repetition rate remains constant, but their duration can vary.
The PWM signal is characterized by such a parameter as the duty cycle or duty cycle. This is the reciprocal of the duty cycle and is equal to the ratio of the pulse duration to its period.
D = (t/T) * 100%
The figures below show PWM signals with different duty cycles.
With this control method, the motor rotation speed will be proportional to the duty cycle of the PWM signal.
Simple DC Motor Control Circuit
The simplest DC motor control circuit consists of a field-effect transistor, the gate of which is supplied with a PWM signal. The transistor in this circuit acts as an electronic switch that switches one of the motor terminals to ground. The transistor opens at the moment of the pulse duration.
How will the engine behave when turned on like this? If the frequency of the PWM signal is low (several Hz), the motor will turn jerkily. This will be especially noticeable with a small duty cycle of the PWM signal.
At a frequency of hundreds of Hz, the motor will rotate continuously and its rotation speed will change in proportion to the duty cycle. Roughly speaking, the engine will “perceive” the average value of the energy supplied to it.
Circuit for generating a PWM signal
There are many circuits for generating a PWM signal. One of the simplest is a circuit based on a 555 timer. It requires a minimum of components, requires no setup and can be assembled in one hour.
The VCC circuit supply voltage can be in the range of 5 - 16 Volts. Almost any diodes can be used as diodes VD1 - VD3.
If you are interested in understanding how this circuit works, you need to refer to the block diagram of the 555 timer. The timer consists of a voltage divider, two comparators, a flip-flop, an open collector switch and an output buffer.
The power supply (VCC) and reset pins are connected to the power supply plus, say +5 V, and the ground pin (GND) to the minus. The open collector of the transistor (DISC pin) is connected to the power supply positive through a resistor and the PWM signal is removed from it. The CONT pin is not used; a capacitor is connected to it. The THRES and TRIG comparator pins are combined and connected to an RC circuit consisting of a variable resistor, two diodes and a capacitor. The middle pin of the variable resistor is connected to the OUT pin. The extreme terminals of the resistor are connected through diodes to a capacitor, which is connected to the ground with the second terminal. Thanks to this inclusion of diodes, the capacitor is charged through one part of the variable resistor and discharged through the other.
At the moment the power is turned on, the OUT pin is at a low logical level, then the THRES and TRIG pins, thanks to the VD2 diode, will also be at a low level. The upper comparator will switch the output to zero, and the lower one to one. The output of the trigger will be set to zero (because it has an inverter at the output), the transistor switch will close, and the OUT pin will be set to a high level (because it has an inverter at the input). Next, capacitor C3 will begin to charge through diode VD1. When it charges to a certain level, the lower comparator will switch to zero, and then the upper comparator will switch the output to one. The trigger output will be set to a unity level, the transistor switch will open, and the OUT pin will be set to a low level. Capacitor C3 will begin to discharge through diode VD2 until it is completely discharged and the comparators switch the trigger to another state. The cycle will then repeat.
The approximate frequency of the PWM signal generated by this circuit can be calculated using the following formula:
F = 1.44/(R1*C1), [Hz]
where R1 is in ohms, C1 is in farads.
With the values indicated in the diagram above, the frequency of the PWM signal will be equal to:
F = 1.44/(50000*0.0000001) = 288 Hz.
PWM DC motor speed controller
Let's combine the two circuits presented above, and we get a simple DC motor speed controller circuit, which can be used to control the engine speed of a toy, robot, micro drill, etc.
VT1 is an n-type field-effect transistor capable of withstanding the maximum motor current at a given voltage and shaft load. VCC1 is from 5 to 16 V, VCC2 is greater than or equal to VCC1.
Instead of a field-effect transistor, you can use a bipolar n-p-n transistor, a Darlington transistor, or an opto-relay of appropriate power.
The DC motor speed controller circuit operates on the principles of pulse width modulation and is used to change the speed of a 12 volt DC motor. Regulating the engine shaft speed using pulse-width modulation gives greater efficiency than simply changing the DC voltage supplied to the engine, although we will also consider these schemes
DC motor speed controller circuit for 12 volts
The motor is connected in a circuit to a field-effect transistor which is controlled by pulse-width modulation carried out on the NE555 timer chip, which is why the circuit turned out to be so simple.
The PWM controller is implemented using a conventional pulse generator on an astable multivibrator, generating pulses with a repetition rate of 50 Hz and built on the popular NE555 timer. The signals coming from the multivibrator create a bias field at the gate of the field-effect transistor. The duration of the positive pulse is adjusted using variable resistance R2. The longer the duration of the positive pulse arriving at the gate of the field-effect transistor, the greater the power supplied to the DC motor. And vice versa, the shorter the pulse duration, the weaker the electric motor rotates. This circuit works great on a 12 volt battery.
DC motor speed control circuit for 6 volts
The speed of the 6 volt motor can be adjusted within 5-95%
Engine speed controller on PIC controller
Speed control in this circuit is achieved by applying voltage pulses of varying duration to the electric motor. For these purposes, PWM (pulse width modulators) are used. In this case, pulse width control is provided by a PIC microcontroller. To control the engine rotation speed, two buttons SB1 and SB2, “More” and “Less,” are used. You can change the rotation speed only when the “Start” toggle switch is pressed. The pulse duration varies, as a percentage of the period, from 30 to 100%.
As a voltage stabilizer for the PIC16F628A microcontroller, a three-pin KR1158EN5V stabilizer is used, which has a low input-output voltage drop, only about 0.6V. The maximum input voltage is 30V. All this allows the use of motors with voltages from 6V to 27V. The KT829A composite transistor is used as a power switch, which is preferably installed on a radiator.
The device is assembled on a printed circuit board measuring 61 x 52 mm. You can download the PCB drawing and firmware file from the link above. (See folder in the archive 027-el)
PWM DC motor speed controller
This DIY circuit can be used as a speed controller for a 12V DC motor with a current rating of up to 5A, or as a dimmer for 12V halogen and LED lamps up to 50W. Control is carried out using pulse width modulation (PWM) at a pulse repetition rate of about 200 Hz. Naturally, the frequency can be changed if necessary, selecting for maximum stability and efficiency.
Most of these structures are assembled according to a much simpler scheme. Here we present a more advanced version that uses a 7555 timer, a bipolar transistor driver and a powerful MOSFET. This design provides improved speed control and operates over a wide load range. This is indeed a very effective scheme and the cost of its parts when purchased for self-assembly is quite low.
PWM controller circuit for 12 V motor
The circuit uses a 7555 Timer to create a variable pulse width of about 200 Hz. It controls transistor Q3 (via transistors Q1 - Q2), which controls the speed of the electric motor or light bulbs.
There are many applications for this circuit that will be powered by 12V: electric motors, fans or lamps. It can be used in cars, boats and electric vehicles, in model railways and so on.
12 V LED lamps, for example LED strips, can also be safely connected here. Everyone knows that LED bulbs are much more efficient than halogen or incandescent bulbs and will last much longer. And if necessary, power the PWM controller from 24 volts or more, since the microcircuit itself with a buffer stage has a power stabilizer.
AC Motor Speed Controller
PWM controller 12 volt
Half Bridge DC Regulator Driver
Mini drill speed controller circuit
Diagrams and overview of 220V electric motor speed controllers
To smoothly increase and decrease the shaft rotation speed, there is a special device - a 220V electric motor speed controller. Stable operation, no voltage interruptions, long service life - the advantages of using an engine speed controller for 220, 12 and 24 volts.
- Why do you need a frequency converter?
- Application area
- Selecting a device
- IF device
- Types of devices
- Triac device
- Proportional Signal Process
Why do you need a frequency converter?
The function of the regulator is to invert the voltage of 12, 24 volts, ensuring smooth start and stop using pulse width modulation.
Speed controllers are included in the structure of many devices, as they ensure the accuracy of electrical control. This allows you to adjust the speed to the desired amount.
Application area
DC motor speed controller is used in many industrial and domestic applications. For example:
- heating complex;
- equipment drives;
- welding machine;
- electric ovens;
- vacuum cleaners;
- Sewing machines;
- washing machines.
Selecting a device
In order to select an effective regulator, it is necessary to take into account the characteristics of the device and its intended purpose.
- Vector controllers are common for commutator motors, but scalar controllers are more reliable.
- An important selection criterion is power. It must correspond to that permitted on the unit used. It is better to exceed for safe operation of the system.
- The voltage must be within acceptable wide ranges.
- The main purpose of the regulator is to convert frequency, so this aspect must be selected according to the technical requirements.
- You also need to pay attention to the service life, dimensions, number of inputs.
IF device
- AC motor natural controller;
- drive unit;
- additional elements.
The circuit diagram of the 12 V engine speed controller is shown in the figure. The speed is adjusted using a potentiometer. If pulses with a frequency of 8 kHz are received at the input, then the supply voltage will be 12 volts.
The device can be purchased at specialized sales points, or you can make it yourself.
AC speed controller circuit
When starting a three-phase motor at full power, current is transmitted, the action is repeated about 7 times. The current bends the motor windings, generating heat over a long period of time. A converter is an inverter that provides energy conversion. The voltage enters the regulator, where 220 volts are rectified using a diode located at the input. Then the current is filtered through 2 capacitors. PWM is generated. Next, the pulse signal is transmitted from the motor windings to a specific sinusoid.
There is a universal 12V device for brushless motors.
To save on electricity bills, our readers recommend the Electricity Saving Box. Monthly payments will be 30-50% less than they were before using the saver. It removes the reactive component from the network, resulting in a reduction in load and, as a consequence, current consumption. Electrical appliances consume less electricity and costs are reduced.
The circuit consists of two parts - logical and power. The microcontroller is located on a chip. This scheme is typical for a powerful engine. The uniqueness of the regulator lies in its use with various types of engines. The circuits are powered separately; the key drivers require 12V power.
Types of devices
Triac device
The triac device is used to control lighting, power of heating elements, and rotation speed.
The controller circuit based on a triac contains a minimum of parts shown in the figure, where C1 is a capacitor, R1 is the first resistor, R2 is the second resistor.
Using a converter, power is regulated by changing the time of an open triac. If it is closed, the capacitor is charged by the load and resistors. One resistor controls the amount of current, and the second regulates the charging rate.
When the capacitor reaches the maximum voltage threshold of 12V or 24V, the switch is activated. The triac goes into the open state. When the mains voltage passes through zero, the triac is locked, and then the capacitor gives a negative charge.
Converters on electronic keys
Common thyristor regulators with a simple operating circuit.
Thyristor, works in alternating current network.
A separate type is the AC voltage stabilizer. The stabilizer contains a transformer with numerous windings.
DC stabilizer circuit
24 volt thyristor charger
To a 24 volt voltage source. The principle of operation is to charge a capacitor and a locked thyristor, and when the capacitor reaches voltage, the thyristor sends current to the load.
Proportional Signal Process
Signals arriving at the system input form feedback. Let's take a closer look using a microcircuit.
Chip TDA 1085
The TDA 1085 chip pictured above provides feedback control of a 12V, 24V motor without loss of power. It is mandatory to contain a tachometer, which provides feedback from the engine to the control board. The stabilization sensor signal goes to a microcircuit, which transmits the task to the power elements - to add voltage to the motor. When the shaft is loaded, the board increases the voltage and the power increases. By releasing the shaft, the tension decreases. The revolutions will be constant, but the power torque will not change. The frequency is controlled over a wide range. Such a 12, 24 volt motor is installed in washing machines.
With your own hands you can make a device for a grinder, wood lathe, sharpener, concrete mixer, straw cutter, lawn mower, wood splitter and much more.
Industrial regulators, consisting of 12, 24 volt controllers, are filled with resin and therefore cannot be repaired. Therefore, a 12V device is often made independently. A simple option using the U2008B chip. The controller uses current feedback or soft start. If the latter is used, elements C1, R4 are required, jumper X1 is not needed, but with feedback, vice versa.
When assembling the regulator, choose the right resistor. Since with a large resistor there may be jerks at the start, and with a small resistor the compensation will be insufficient.
Important! When adjusting the power controller, you need to remember that all parts of the device are connected to the AC network, so safety precautions must be observed!
Speed controllers for single-phase and three-phase 24, 12 volt motors are a functional and valuable device, both in everyday life and in industry.
ENGINE SPEED CONTROL DIAGRAM
Regulator for AC motor
Based on the powerful triac BT138-600, you can assemble a circuit for an AC motor speed controller. This circuit is designed to regulate the rotation speed of electric motors of drilling machines, fans, vacuum cleaners, grinders, etc. The motor speed can be adjusted by changing the resistance of potentiometer P1. Parameter P1 determines the phase of the trigger pulse, which opens the triac. The circuit also performs a stabilization function, which maintains engine speed even under heavy load.
Schematic diagram of an AC motor regulator
For example, when the motor of a drilling machine slows down due to increased metal resistance, the EMF of the motor also decreases. This leads to an increase in voltage in R2-P1 and C3 causing the triac to open for a longer time, and the speed increases accordingly.
Regulator for DC motor
The simplest and most popular method of adjusting the rotation speed of a DC motor is based on the use of pulse width modulation ( PWM or PWM ). In this case, the supply voltage is supplied to the motor in the form of pulses. The repetition rate of the pulses remains constant, but their duration can change - so the speed (power) also changes.
To generate a PWM signal, you can take a circuit based on the NE555 chip. The simplest circuit of a DC motor speed controller is shown in the figure:
Schematic diagram of a constant power electric motor regulator
Here VT1 is an n-type field-effect transistor capable of withstanding the maximum motor current at a given voltage and shaft load. VCC1 is from 5 to 16 V, VCC2 is greater than or equal to VCC1. The frequency of the PWM signal can be calculated using the formula:
where R1 is in ohms, C1 is in farads.
With the values indicated in the diagram above, the frequency of the PWM signal will be equal to:
F = 1.44/(50000*0.0000001) = 290 Hz.
It is worth noting that even modern devices, including those with high control power, are based on precisely such circuits. Naturally, using more powerful elements that can withstand higher currents.
PWM - engine speed controllers on timer 555
The 555 timer is widely used in control devices, for example, in PWM - speed controllers for DC motors.
Anyone who has ever used a cordless screwdriver has probably heard a squeaking sound coming from inside. This is the whistling of the motor windings under the influence of the pulse voltage generated by the PWM system.
It is simply indecent to regulate the speed of an engine connected to a battery in another way, although it is quite possible. For example, simply connect a powerful rheostat in series with the motor, or use an adjustable linear voltage regulator with a large radiator.
A variant of the PWM regulator based on the 555 timer is shown in Figure 1.
The circuit is quite simple and is based on a multivibrator, albeit converted into a pulse generator with an adjustable duty cycle, which depends on the ratio of the charge and discharge rates of capacitor C1.
The capacitor is charged through the circuit: +12V, R1, D1, the left side of the resistor P1, C1, GND. And the capacitor is discharged along the circuit: upper plate C1, right side of resistor P1, diode D2, pin 7 of the timer, bottom plate C1. By rotating the slider of resistor P1, you can change the ratio of the resistances of its left and right parts, and therefore the charging and discharging time of capacitor C1, and, as a consequence, the duty cycle of the pulses.
Figure 1. PWM circuit - regulator on a 555 timer
This scheme is so popular that it is already available in the form of a set, as shown in the following figures.
Figure 2. Schematic diagram of a set of PWM regulators.
Timing diagrams are also shown here, but, unfortunately, the part values are not shown. They can be seen in Figure 1, which is why it is shown here. Instead of bipolar transistor TR1, without altering the circuit, you can use a powerful field effect one, which will increase the load power.
By the way, another element has appeared in this diagram - diode D4. Its purpose is to prevent the discharge of the timing capacitor C1 through the power source and load - the motor. This ensures stabilization of the PWM frequency.
By the way, with the help of such circuits you can control not only the speed of a DC motor, but also simply an active load - an incandescent lamp or some kind of heating element.
Figure 3. Printed circuit board of a PWM regulator set.
If you put in a little work, it is quite possible to recreate this using one of the programs for drawing printed circuit boards. Although, given the small number of parts, it will be easier to assemble one copy using a hinged installation.
Figure 4. Appearance of a set of PWM regulators.
True, the already assembled branded set looks quite nice.
Here, perhaps, someone will ask a question: “The load in these regulators is connected between +12V and the collector of the output transistor. But what about, for example, in a car, because everything there is already connected to the ground, the body, of the car?”
Yes, you can’t argue against the mass; here we can only recommend moving the transistor switch to the “positive” gap; wires. A possible version of such a scheme is shown in Figure 5.
Figure 6 shows the MOSFET output stage separately. The drain of the transistor is connected to the +12V battery, the gate just hangs 9raquo; in the air (which is not recommended), a load is connected to the source circuit, in our case a light bulb. This figure is shown simply to explain how a MOSFET transistor works.
In order to open a MOSFET transistor, it is enough to apply a positive voltage to the gate relative to the source. In this case, the light bulb will light up at full intensity and will shine until the transistor is closed.
In this figure, the easiest way to turn off the transistor is to short-circuit the gate to the source. And such a manual closure is quite suitable for checking the transistor, but in a real circuit, especially a pulse circuit, you will have to add a few more details, as shown in Figure 5.
As mentioned above, an additional voltage source is required to turn on the MOSFET transistor. In our circuit, its role is played by capacitor C1, which is charged via the +12V circuit, R2, VD1, C1, LA1, GND.
To open transistor VT1, a positive voltage from a charged capacitor C2 must be applied to its gate. It is quite obvious that this will only happen when transistor VT2 is open. And this is only possible if the optocoupler transistor OP1 is closed. Then the positive voltage from the positive plate of capacitor C2 through resistors R4 and R1 will open transistor VT2.
At this moment, the input PWM signal must be at a low level and bypass the optocoupler LED (this LED switching is often called inverse), therefore, the optocoupler LED is off and the transistor is closed.
To turn off the output transistor, you need to connect its gate to the source. In our circuit, this will happen when transistor VT3 opens, and this requires that the output transistor of the optocoupler OP1 be open.
The PWM signal at this time is at a high level, so the LED is not shunted and emits the infrared rays assigned to it, the optocoupler transistor OP1 is open, which as a result turns off the load - the light bulb.
One of the options for using such a scheme in a car is daytime running lights. In this case, motorists claim to use high beam lamps turned on at full intensity. Most often these designs are on a microcontroller. There are a lot of them on the Internet, but it’s easier to do it on the NE555 timer.
j&;electrician Ino - electrical engineering and electronics, home automation, l&;articles about the construction and repair of home electrical wiring, sockets and switches, wires and cables, and sources l&;veta, interesting acts and much more for electricians and home builders.
Information and training materials for other electricians.
Keys, examples and technical solutions, overviews of interesting electrical innovations.
The information on the site j&;electrician is provided in informational and educational documents. The administration of the site is not responsible for the use of this information. Sai can l&;obtain materials 12+
Reproduction of l&;ite k&;materials is prohibited.